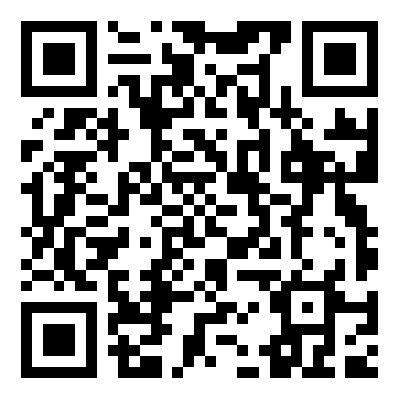
-
Chicken Glasses
Chicken Glasses for Anti-Fighting, Anti-Pecking & Anti-Toe-Pecking...
-
Water Level Controller
Water Level Indicator is a device designed to monitor the liquid level (e.g., water, oil) in a tank ...
-
Water Level Controller
Water Level Indicator is a device designed to monitor the liquid level (e.g., water, oil) in a tank ...
-
Hay Feeder
Hay Feeder – Product Introduction Product Overview A Hay Feeder is a specialized equipment designed...
-
Hay Feeder
Hay Feeder – Product Introduction Product Overview A Hay Feeder is a specialized equipment designed...
The processing technology flow of metal stretching parts
Apr 12
2025
The processing technology of metal stretching parts generally includes the following steps:
Design drawings: Based on factors such as the shape, size, precision requirements, and production batch of the product, design reasonable stretching part drawings. The drawings should clearly indicate the technical requirements such as dimensions, tolerances, and surface roughness of each part.
Material selection: Choose suitable hardware materials based on the usage requirements and performance characteristics of the stretching parts. Common materials include low-carbon steel, stainless steel, copper, aluminum, etc. The performance indicators such as thickness, hardness, and ductility of the material need to meet the requirements of the stretching process.
Cutting: Cut the selected hardware materials according to the design dimensions to obtain the desired blank. There are various cutting methods, such as shearing machine cutting, laser cutting, punching, etc.
Pre stretching treatment: necessary pre-treatment of the blank, such as cleaning, deburring, and applying lubricants. Cleaning is to remove oil stains, impurities, etc. on the surface of materials to ensure the smooth progress of the stretching process; Deburring can prevent burrs from affecting product quality or damaging the mold during the stretching process; Applying lubricants can effectively reduce the friction coefficient between materials and molds, reduce wear, and improve the surface quality of stretched parts.
Stretch forming: By applying pressure to the blank through stretching molds and stamping equipment, it undergoes plastic deformation and gradually forms the desired shape of the stretched part. During the stretching process, it is necessary to control the stretching ratio, stretching speed, edge pressure and other process parameters reasonably according to the characteristics of the material and the shape, size and other factors of the stretched part, in order to avoid defects such as tearing and wrinkling.
Edge trimming and shaping: The stretched workpiece may have some irregular parts at the edges, or there may be certain deviations in shape and size from the design requirements, which need to be corrected through edge trimming and shaping processes. Edge trimming is the process of removing excess material from the edges of stretched parts to make them neat and smooth; Plastic surgery is the fine-tuning of the overall shape and size of the stretched part to meet the precision requirements of the product.
Surface treatment: In order to improve the corrosion resistance, wear resistance, decorative properties, and other properties of the stretched parts, surface treatment is required. Common surface treatment methods include electroplating, spraying, oxidation, etc.
Quality inspection: Conduct comprehensive quality inspection on the processed metal stretching parts, including appearance inspection, dimensional accuracy measurement, surface quality testing, mechanical performance testing, etc. Through inspection, select unqualified products, analyze the reasons, and take corresponding improvement measures to ensure that the product quality meets the design requirements.
Packaging and storage: Packaging the qualified stretching parts to prevent damage during transportation and storage. The packaging method is usually selected based on the characteristics of the product and customer requirements, such as using packaging materials such as plastic bags, paper boxes, wooden boxes, etc. Packaged products are stored in the warehouse and waiting for shipment.