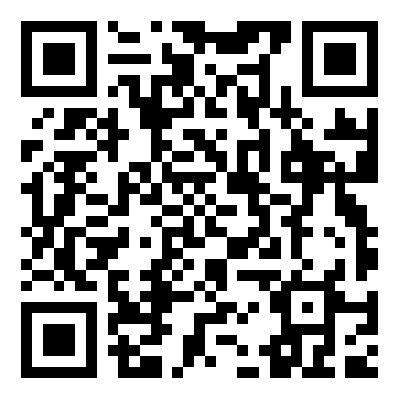
-
Chicken Glasses
Chicken Glasses for Anti-Fighting, Anti-Pecking & Anti-Toe-Pecking...
-
Water Level Controller
Water Level Indicator is a device designed to monitor the liquid level (e.g., water, oil) in a tank ...
-
Water Level Controller
Water Level Indicator is a device designed to monitor the liquid level (e.g., water, oil) in a tank ...
-
Hay Feeder
Hay Feeder – Product Introduction Product Overview A Hay Feeder is a specialized equipment designed...
-
Hay Feeder
Hay Feeder – Product Introduction Product Overview A Hay Feeder is a specialized equipment designed...
Can the accuracy of stretching parts be improved through post-processing?
Apr 12
2025
The accuracy of stretched parts can be improved to some extent through post-processing, and common post-processing methods include the following:
machining
Turning: For stretched parts that require high precision in outer or inner diameter dimensions after stretching, turning can be used to accurately control their diameter dimensions, effectively correcting dimensional deviations generated during the stretching process and improving the accuracy of geometric tolerances such as cylindricity. For example, some cylindrical stretching parts in car engines can achieve an outer diameter accuracy of within ± 0.01mm after turning.
Grinding: Grinding is an effective machining method when the surface roughness and flatness requirements of the stretched part are high. It can remove the small unevenness on the surface of the stretched parts, making the surface roughness reach Ra0.8-Ra0.2 μ m or even lower, while improving the flatness accuracy. It is commonly used in the later processing of stretched parts such as precision instrument casings and mold cavities.
Boring: For some high-precision holes on stretching parts, boring machining can accurately ensure the diameter size accuracy, cylindricity, and positional accuracy of the hole with other surfaces. On the fuel nozzle stretching parts of aircraft engines, the diameter accuracy of the injection holes can be controlled within ± 0.05mm by boring, meeting its high-precision injection requirements.
Surface Treatment
Electroplating: Electroplating can not only improve the corrosion resistance and wear resistance of stretched parts, but also improve their surface roughness and dimensional accuracy to a certain extent. By uniformly depositing the electroplating layer, small defects on the surface of the stretched part can be filled, making the surface smoother. At the same time, the thickness of the electroplating layer can be precisely controlled, which has a certain fine-tuning effect on the dimensional accuracy of the stretched part. For example, after electroplating, the surface roughness of some electronic device casing stretching parts can be reduced from Ra3.2 μ m to Ra1.6 μ m, and the dimensional accuracy can be controlled within ± 0.05mm.
Chemical plating: Similar to electroplating, chemical plating can also improve the surface properties and accuracy of stretched parts. Chemical nickel phosphorus alloy plating and other processes can obtain uniform and dense coatings, improve the hardness and wear resistance of the surface of the stretched parts, and also help control the dimensional accuracy, especially suitable for stretched parts with complex shapes that are difficult to use electroplating processes.
Polishing: Polishing is a common method to improve the surface quality and accuracy of stretched parts. By mechanical polishing, electrolytic polishing and other methods, the oxide scale, burrs and scratches on the surface of the stretched part can be removed, greatly reducing the surface roughness and achieving high smoothness, thereby improving the appearance quality and dimensional accuracy of the stretched part. For example, some decorative stretching parts can achieve a surface roughness of Ra0.1 μ m or less after polishing, making the appearance more beautiful and the dimensional accuracy can also be improved to a certain extent.
plastic surgery
Cold forming: For some stretch parts that require high shape accuracy, cold forming is an effective method. By using specialized shaping molds, a certain amount of pressure is applied to the stretched part at room temperature to induce local plastic deformation, thereby correcting the shape deviation generated during the stretching process and improving shape accuracy. For example, after cold forming, the flatness of some car cover stretching parts can be controlled within ± 0.5mm.
Hot forming: For some high-strength materials or complex shaped stretched parts, cold forming may encounter difficulties, and hot forming technology can be used in this case. Heating the stretched part to a certain temperature for shaping increases the plasticity of the material at high temperatures, making it easier to adjust the shape through molds and improve accuracy. But thermal shaping requires precise control of parameters such as heating temperature, holding time, and cooling rate to avoid affecting material properties.
However, there are also certain limitations to improving accuracy in post-processing, such as limitations in material properties, processing costs, and feasibility of processing techniques. For some highly precise stretching parts, relying solely on post-processing may not fully meet the requirements, and strict control and optimization are needed in the early stages such as stretching process design, mold manufacturing, and material selection.