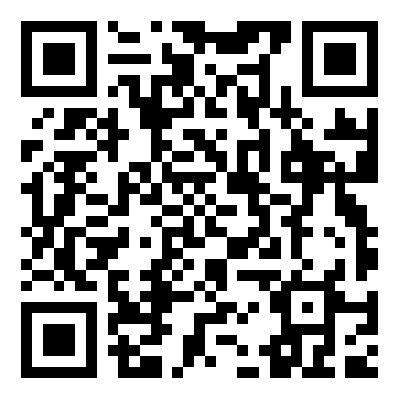
-
Chicken Glasses
Chicken Glasses for Anti-Fighting, Anti-Pecking & Anti-Toe-Pecking...
-
Water Level Controller
Water Level Indicator is a device designed to monitor the liquid level (e.g., water, oil) in a tank ...
-
Water Level Controller
Water Level Indicator is a device designed to monitor the liquid level (e.g., water, oil) in a tank ...
-
Hay Feeder
Hay Feeder – Product Introduction Product Overview A Hay Feeder is a specialized equipment designed...
-
Hay Feeder
Hay Feeder – Product Introduction Product Overview A Hay Feeder is a specialized equipment designed...
What are the common problems in metal accessory processing?
Apr 15
2025
Problems encountered in metal accessory processing:
1. When stamping and bending soft materials such as copper and aluminum alloys in continuous operation, metal particles or residues are prone to adhere to the surface of the working area, causing large scratches on the object. At this time, carefully analyze the shape and lubricating oil of the working area to generate particles and residues in the blank without causing scratches.
2. The gap between the convex and concave molds should not be too small, as a small gap can cause thinning and scratching. During the stamping process, it is necessary to constantly check the changes in the clearance of the mold.
3. When the convex mold enters the concave mold too much, it will cause scratches on the surface of the parts. Therefore, without being affected by rebound, the amount of convex mold entering the concave mold should be appropriately reduced.
4. The radius of the concave die corner is too small, and there are impact marks on the bent part of the metal stamping. Polishing the concave die and increasing the fillet radius of the concave die can prevent scratches on metal stamping bent parts.
5. When the burr surface is used as the outer surface for metal stamping and bending, the workpiece is prone to cracking and scratching; Therefore, when metal stamping and bending, the burr surface should be used as the inner surface of the metal stamping and bending.
6. In order to meet the requirements of wood processing accuracy, the metal stamping and bending method of bottom stamping material is often used. Therefore, when metal stamping bends, the springs, position pin holes, plate and return holes on the raw material plate are affected. Becoming an indentation, therefore, adjustments should be made.
7. When the bending direction of metal stamping is parallel to the rolling direction of the material, cracks will appear on the surface of the part, thereby reducing the surface quality of the workpiece. When the metal stamping bending exceeds two parts, the angle between the metal stamping bending direction and the rolling direction should be maximized.
In the production process of general metal accessories, there are four processing techniques:
1. Bending: The stamping process of bending a sheet metal into an angle and shape along a curved line.
2. Local forming: a stamping process that uses various types of local deformations to change the shape of a blank or metal component (including flanging, bulging, leveling, and adjustment processes, etc.).
3. Deep drawing: a stamping process that transforms flat sheet metal into various open hollow parts, or further changes the shape and size of hollow parts.
4. Punching: a stamping process that separates sheet metal, including punching, cutting, trimming, and sectioning.
The flipping and twisting of metal parts during stamping are caused by the method of punching and cutting the remaining material around the metal parts in the progressive die to form the shape of the stamped parts. The main reason for the flipping and twisting of punched parts is the influence of punching force. During punching, due to the presence of punching gaps, the material is stretched on one side of the die (warping upwards) and compressed on the side closer to the punch. When using a discharge plate, use the discharge plate to press the material tightly to prevent the material on the concave mold side from warping upwards. At this time, the stress condition of the material changes accordingly. As the unloading plate increases its compression force, the material on the convex mold side is stretched (the compression force tends to decrease), while the material on the concave mold surface is compressed (the tensile force tends to decrease). The flipping of metal accessories is caused by the material on the concave mold surface being stretched. So when punching, pressing and compressing the material is the main way to prevent the workpiece from flipping or twisting.
The production rate of metal parts processing is good, the operation is simple, and it is easy to achieve mechanization and automation. The advantages of metal parts processing are:
1. Metal accessory processing has a good production rate, simple operation, and is easy to achieve mechanization and automation. This is because metal stamping molds and equipment rely on precision machining, with up to dozens of strokes per minute. Generally, according to numbers, the pressure can reach hundreds or even thousands of times higher per minute, and each stamping stroke may result in one stamping.
2. Metal stamping processing has a wide range of dimensions and complex shapes for parts such as small clock stopwatches, car longitudinal beams, and coverings. In addition, the cold deformation hardening effect of metal stamping materials results in high punching strength and stiffness.
3. Metal accessories generally have no chips, low material consumption, and do not require any heating equipment. The processing method of the present invention can save materials and energy.
4. The determination of metal stamping molds is based on the dimensional accuracy and shape accuracy of metal accessories, which generally do not damage the surface quality of the metal stamping molds and have a long service life. Therefore, the quality of metal stamping is not chaotic and the interchangeability is good.
The principles of metal accessory design are as follows:
1. The metal accessories designed should be conducive to processing them using existing equipment, process equipment, and process flow as much as possible, and to extending the service life of the stamping die.
2. The designed metal accessories achieve product usage and technical performance, and are easy to assemble and repair.
3. The metal fittings designed have a simple shape and correct structure, which is conducive to simplifying the mold structure and reducing the number of processes. That is, using fewer stamping processes to complete the entire part processing, reducing the need for other methods of processing, and facilitating stamping operations. This facilitates the organization to achieve mechanization and automation production, thereby improving labor productivity.
4. The metal accessories designed should have lower requirements for dimensional accuracy and surface roughness levels as much as possible under normal use, and be conducive to product interchangeability, reducing waste and ensuring stable product quality.
5. The design of metal accessories is beneficial for improving the utilization rate of metal materials, reducing the variety and specifications of materials, and minimizing material consumption as much as possible. If possible, use inexpensive materials to achieve zero waste and minimal waste cutting of parts.