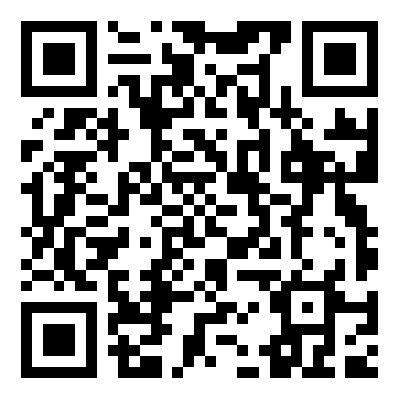
金属配件加工中常见的问题有哪些?
Apr 15
2025
金属配件加工中遇到的问题:
1.在连续操作中冲压和弯曲铜、铝合金等软材料时,金属颗粒或残留物容易附着在工作区域的表面,导致物体上出现大划痕。此时,仔细分析工作区域的形状和润滑油,在毛坯中产生颗粒和残留物,而不会造成划痕。
2.凸模和凹模之间的间隙不应太小,因为小间隙会导致变薄和划伤。在冲压过程中,需要不断检查模具间隙的变化。
当凸模过多地进入凹模时,会导致零件表面产生划痕。因此,在不受回弹影响的情况下,应适当减少凸模进入凹模的量。
4.凹模拐角的半径太小,金属冲压的弯曲部分有冲击痕迹。抛光凹模并增加凹模的圆角半径可以防止金属冲压弯曲零件上的划痕。
5.当毛刺表面用作金属冲压和弯曲的外表面时,工件容易开裂和划伤;因此,在金属冲压和弯曲时,应将毛刺表面用作金属冲压和弯折的内表面。
6.为了满足木材加工精度的要求,经常使用底部冲压材料的金属冲压和弯曲方法。因此,当金属冲压弯曲时,原材料板上的弹簧、定位销孔、板和回位孔都会受到影响。因此,如果成为压痕,则应进行调整。
7.当金属冲压的弯曲方向与材料的轧制方向平行时,零件表面会出现裂纹,从而降低工件的表面质量。当金属冲压弯曲超过两个部分时,金属冲压弯曲方向与轧制方向之间的角度应最大化。
在一般金属配件的生产过程中,有四种加工技术:
1.弯曲:将金属板沿曲线弯曲成角度和形状的冲压工艺。
2.局部成形:一种利用各种局部变形来改变毛坯或金属部件形状的冲压工艺(包括翻边、鼓包、校平和调整工艺等)。
3.深冲压:将平板金属转化为各种开放式空心零件,或进一步改变空心零件形状和尺寸的冲压工艺。
4.冲压:一种分离金属板的冲压工艺,包括冲压、切割、修整和分段。
冲压过程中金属零件的翻转和扭曲是由在级进模中冲压和切割金属零件周围的剩余材料以形成冲压零件形状的方法引起的。冲压件翻转和扭曲的主要原因是冲压力的影响。在冲压过程中,由于存在冲压间隙,材料在模具的一侧被拉伸(向上翘曲),在靠近冲头的一侧被压缩。使用放料板时,用放料板将材料压紧,防止凹模侧的材料向上翘曲。此时,材料的应力状态相应地发生了变化。随着卸载板压缩力的增加,凸模侧的材料被拉伸(压缩力趋于减小),而凹模表面的材料被压缩(张力趋于减小)。金属配件的翻转是由凹模表面上的材料被拉伸引起的。因此,在冲压时,压制和压缩材料是防止工件翻转或扭曲的主要方法。
金属零件加工的生产率高,操作简单,易于实现机械化和自动化。金属零件加工的优点是:
1.金属配件加工生产率好,操作简单,易于实现机械化和自动化。这是因为金属冲压模具和设备依赖于精密加工,每分钟可达数十次行程。一般来说,根据数字,压力每分钟可以高出数百甚至数千倍,每次冲压行程可能导致一次冲压。
2.对于小型钟表秒表、汽车纵梁和覆盖物等零件,金属冲压加工具有广泛的尺寸和复杂的形状。此外,金属冲压材料的冷变形硬化效应导致了较高的冲压强度和刚度。
3.金属配件一般无切屑,材料消耗低,不需要任何加热设备。本发明的加工方法可以节省材料和能源。
4.五金冲压模具的确定是基于金属配件的尺寸精度和形状精度,一般不会损害五金冲压模具表面质量,使用寿命长。因此,金属冲压的质量不混乱,互换性好。
金属配件设计的原则如下:
1.设计的金属配件应尽可能有利于使用现有设备、工艺设备和工艺流程进行加工,并延长冲压模具的使用寿命。
2.设计的金属配件达到了产品使用和技术性能,易于组装和维修。
3.设计的金属配件形状简单,结构正确,有利于简化模具结构,减少工序数量。也就是说,使用更少的冲压工艺来完成整个零件加工,减少了对其他加工方法的需求,并方便了冲压操作。这有利于组织实现机械化和自动化生产,从而提高劳动生产率。
4.设计的金属配件在正常使用情况下应尽可能降低对尺寸精度和表面粗糙度的要求,有利于产品互换性,减少浪费,保证产品质量稳定。
5.金属配件的设计有利于提高金属材料的利用率,减少材料的品种和规格,尽可能减少材料消耗。如果可能的话,使用廉价的材料来实现零浪费和最小的零件切割浪费。