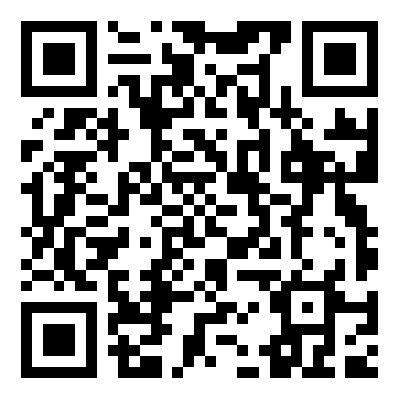
-
Chicken Glasses
Chicken Glasses for Anti-Fighting, Anti-Pecking & Anti-Toe-Pecking...
-
Water Level Controller
Water Level Indicator is a device designed to monitor the liquid level (e.g., water, oil) in a tank ...
-
Water Level Controller
Water Level Indicator is a device designed to monitor the liquid level (e.g., water, oil) in a tank ...
-
Hay Feeder
Hay Feeder – Product Introduction Product Overview A Hay Feeder is a specialized equipment designed...
-
Hay Feeder
Hay Feeder – Product Introduction Product Overview A Hay Feeder is a specialized equipment designed...
Quality inspection method for hardware stretching parts
Apr 12
2025
The quality inspection of hardware stretching parts is a key link to ensure that the product meets design requirements and performance. The inspection method should cover multiple aspects such as dimensional accuracy, surface quality, and mechanical properties. The following are quality inspection methods for hardware stretching parts:
1、 Dimensional accuracy testing
Measuring tool detection
Use tools such as vernier calipers, micrometers, height gauges, etc. to measure the key dimensions of the stretched parts (such as length, width, thickness, diameter, etc.) to ensure compliance with design tolerance requirements.
For complex shapes, a coordinate measuring machine (CMM) can be used for three-dimensional dimension inspection to ensure that the form and position tolerances (such as flatness, roundness, perpendicularity) meet the standards.
Special inspection tools for testing
For mass production, design specialized gauges (such as plug gauges, ring gauges, and card plates) for rapid inspection to improve efficiency.
2、 Surface quality inspection
visual inspection
Check the surface of the stretched part for defects such as cracks, scratches, oxidation, wrinkling, and dents.
Use a magnifying glass or industrial endoscope to magnify and observe minor defects.
Surface roughness detection
Measure the Ra value (arithmetic mean deviation) of the stretched surface using a surface roughness meter to ensure compliance with design requirements (such as Ra ≤ 0.8 μ m).
NDT
Magnetic particle inspection: detecting surface and near surface cracks.
Penetrant testing: detecting surface opening defects.
Eddy current testing: detecting surface and subsurface defects, suitable for conductive materials.
3、 Mechanical performance testing
Tensile test
Prepare standard specimens, apply tension on a tensile testing machine, record parameters such as tensile strength, yield strength, elongation, etc., and evaluate the mechanical properties of the material.
Hardness test
Use a Rockwell hardness tester, Vickers hardness tester, or Brinell hardness tester to measure the hardness of the stretched parts to ensure compliance with material hardness requirements.
Metallographic Analysis
Take samples and observe them under a metallographic microscope to analyze the grain size, microstructure, and defects (such as inclusions and segregation) of the material.
4、 Functional performance testing
Sealing test
Perform airtightness or liquid tightness tests on the stretched parts to ensure no leaks (such as using a helium mass spectrometer leak detector or pressure decay method).
Corrosion resistance test
Conduct salt spray test, wet heat test or immersion test to evaluate the corrosion resistance of tensile components in specific environments.
fatigue test
Test the fatigue life of the tensile component under alternating load to ensure that it meets the design and usage requirements.
5、 Material composition analysis
spectral analysis
Use a spectrometer to detect the chemical composition of the stretched material to ensure compliance with material standards (such as Cr and Ni content testing for stainless steel).
Energy dispersive spectroscopy (EDS) analysis
Combining scanning electron microscopy (SEM) for micro area composition analysis to detect impurities or abnormal elements in materials.
6、 Automated detection technology
machine vision inspection
Using high-resolution cameras and image processing algorithms, automatically detect the size, surface defects, and assembly status of stretched parts.
Laser scanning detection
Use a laser scanner to create 3D models of stretched parts, quickly obtain dimensional data, and generate inspection reports.
Online detection system
Integrate sensors and detection equipment on the production line to achieve real-time detection and data feedback of stretched parts.
7、 Testing records and traceability
Record all test results in detail, including testing methods, equipment, personnel, time, and result determination.
Establish a quality traceability system to ensure that each stretch piece can be traced back to the raw material batch, production process, and testing data.