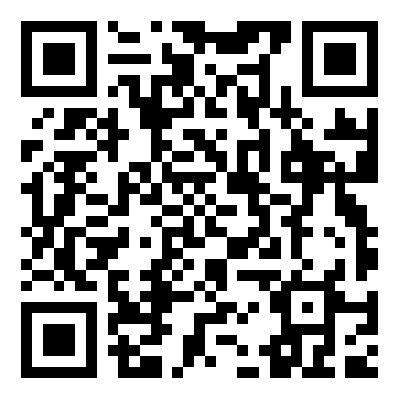
多重拉伸过程的具体操作步骤是什么?
Apr 12
2025
多次拉伸过程是将扁平坯料逐渐拉伸成所需形状和尺寸的复杂零件的过程。具体操作步骤如下:
初始坯料准备:根据零件的尺寸和形状要求计算并切割合适的扁平坯料。坯料的尺寸通常考虑了多次拉伸过程中的材料流动和变形,通常大于最终零件的尺寸。例如,对于圆形拉伸部件,坯料的直径可能是最终部件直径的2-3倍,具体取决于拉伸部件的复杂性和材料特性。
第一次拉伸:将准备好的毛坯放入拉伸模具中,通过压力机施加一定量的压力,使毛坯在凸凹模具的作用下开始变形,形成初步的拉伸形状,如浅杯形。在第一次拉伸过程中,重要的是控制拉伸系数,通常在0.5-0.7之间,以确保均匀的材料流动,避免过度变薄或撕裂。同时,有必要合理调整边缘压力,以防止坯料在拉伸过程中起皱。
中间退火处理(如有必要):如果材料在第一次拉伸后发生加工硬化,导致韧性降低并阻碍后续拉伸,则需要进行中间退火处理。将拉伸的工件加热到适当的温度,保持一段时间,然后缓慢冷却以恢复材料';s微观结构软化状态,改善材料';并促进后续的拉伸过程。例如,对于一些高强度合金钢受拉件,在第一次拉伸后可能需要进行应力消除退火,退火温度一般在600-700℃左右。
后续拉伸:将经过中间处理的工件(如果有的话)放入下一级拉伸模具中进行进一步拉伸。拉伸系数随着每次拉伸而逐渐减小,通常在0.7-0.85之间。随着拉伸次数的增加,工件的形状逐渐接近最终产品的形状。在每次拉伸过程中,应注意控制拉伸速度和边缘压力等工艺参数,以确保拉伸过程的稳定性和工件的质量。例如,对于深圆柱形零件,可能需要拉伸3-5次,每次拉伸后工件的高度逐渐增加,直径逐渐减小。
尺寸和形状调整:在多次拉伸过程中,工件的尺寸和形状可能会出现偏差,需要进行适当的调整。这可以通过调整间隙、圆角半径或改变模具的拉伸工艺参数来实现。例如,如果发现工件的圆柱壁厚度不均匀,可以通过调整凸模和凹模之间的间隙来改善;如果工件的口部膨胀或收缩,可以通过调整拉伸模具的圆角半径来纠正。
最终成形:经过多次拉伸,工件基本达到了所需的形状和尺寸,但仍可能存在一些微小的形状误差或表面不平整问题。此时,最终的成型过程需要使用成型模具对工件施加一定量的压力,使其在模具的作用下发生轻微的塑性变形,进一步提高工件的尺寸和形状精度,使工件表面更光滑。例如,对于一些对外观质量要求较高的拉伸零件,最终成形可以使工件的平面度在±0.1mm以内,表面粗糙度达到Ra0.8-Ra1.6μm。
质量检查:对最终拉伸零件进行全面的质量检查,包括目视检查、尺寸精度测量和性能测试。外观检查主要检查裂纹、划痕、皱纹等缺陷;尺寸精度测量使用卡尺、千分尺、坐标测量仪器等测量工具测量关键尺寸,确保尺寸偏差在设计要求的公差范围内;性能测试是根据拉伸件的使用要求进行的,如硬度测试、强度测试、韧性测试等,以确保拉伸件能够满足实际使用的性能要求。