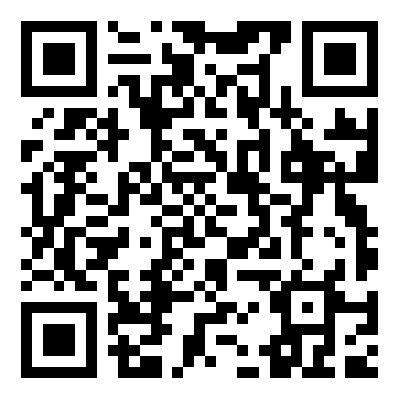
通过后处理可以提高拉伸零件的精度吗?
Apr 12
2025
通过后处理可以在一定程度上提高拉伸零件的精度,常见的后处理方法包括以下几种:
制造
车削:对于拉伸后需要高精度外径或内径尺寸的拉伸零件,车削可用于精确控制其直径尺寸,有效校正拉伸过程中产生的尺寸偏差,提高圆柱度等几何公差的精度。例如,汽车发动机中的一些圆柱形拉伸部件在车削后可以达到±0.01mm以内的外径精度。
磨削:当拉伸零件的表面粗糙度和平整度要求较高时,磨削是一种有效的加工方法。它可以消除拉伸零件表面的小不平坦,使表面粗糙度达到Ra0.8-Ra0.2μm甚至更低,同时提高了平面度精度。它通常用于精密仪器外壳和模具腔等拉伸零件的后期加工。
镗削:对于拉伸零件上的一些高精度孔,镗削加工可以精确地保证孔与其他表面的直径尺寸精度、圆柱度和位置精度。在飞机发动机的燃油喷嘴拉伸部件上,通过钻孔可以将喷射孔的直径精度控制在±0.05mm以内,满足其高精度喷射要求。
表面处理
电镀:电镀不仅可以提高拉伸件的耐腐蚀性和耐磨性,还可以在一定程度上提高其表面粗糙度和尺寸精度。通过均匀沉积电镀层,可以填充拉伸部件表面的小缺陷,使表面更光滑。同时,电镀层的厚度可以精确控制,这对拉伸部件的尺寸精度有一定的微调作用。例如,电镀后,一些电子设备外壳拉伸部件的表面粗糙度可以从Ra3.2μm降低到Ra1.6μm,尺寸精度可以控制在±0.05mm以内。
化学镀:与电镀类似,化学镀也可以提高拉伸零件的表面性能和精度。化学镀镍磷合金等工艺可以获得均匀致密的涂层,提高拉伸零件表面的硬度和耐磨性,也有助于控制尺寸精度,特别适用于形状复杂、难以使用电镀工艺的拉伸零件。
抛光:抛光是提高拉伸零件表面质量和精度的常用方法。通过机械抛光、电解抛光等方法,可以去除拉伸部件表面的氧化皮、毛刺和划痕,大大降低表面粗糙度,实现高光滑度,从而提高拉伸部件的外观质量和尺寸精度。例如,一些装饰性拉伸部件在抛光后可以达到Ra0.1μm或更低的表面粗糙度,使外观更加美观,尺寸精度也可以在一定程度上得到提高。
整形手术
冷成型:对于一些需要高形状精度的拉伸零件,冷成型是一种有效的方法。通过使用专用的成型模具,在室温下对拉伸部件施加一定量的压力,以引起局部塑性变形,从而校正拉伸过程中产生的形状偏差,提高形状精度。例如,冷成型后,一些汽车覆盖物拉伸部件的平面度可以控制在±0.5mm以内。
热成型:对于一些高强度材料或形状复杂的拉伸零件,冷成型可能会遇到困难,在这种情况下可以使用热成型技术。将拉伸部分加热到一定温度进行成型,可以提高材料在高温下的塑性,使其更容易通过模具调整形状并提高精度。但热成型需要精确控制加热温度、保温时间和冷却速率等参数,以避免影响材料性能。
然而,在提高后处理精度方面也存在某些局限性,例如材料性能、加工成本和加工技术可行性方面的局限性。对于一些高精度拉伸零件,仅依靠后处理可能无法完全满足要求,在拉伸工艺设计、模具制造和材料选择等早期阶段需要严格控制和优化。